EZ-MILL PRO
EZ-MILL Pro extends the standard EZ-MILL capabilities to meet the demanding needs of the prototype, tooling, die and mold professional. EZ-MILL Pro includes all the functionality of EZ-MILL plus surface creation and machining capabilities. 3D Surface Machining Wizard combines 12 different Roughing, Re-Roughing and Finishing strategies under a new and simple-to-use dialog box.
$3,995.00
3D Machining Workstep Wizard – CNC Milling Software
We have added a new 3D Surface Machining Wizard to the Machining menu. Beside many cycle related improvements, this new wizard now serves as the foundation for all 3D surface machining by combining all options under a new and simple-to-use dialog interface. It provides an easy to understand choice of methods and toolpath types which allow even inexperienced users to generate their first 3D toolpaths with a couple of clicks.
CNC 3D Machining Strategies – Best CNC Milling Software
Roughing – CNC Milling
The Roughing methods use a horizontal slicing strategy to create machining regions in which a conventional 2.5 axis toolpath is generated. The selected Cut surfaces are offset in 3D by the specified tool then sliced at each Z Step interval. Intersection boundaries resulting from cavities or depressions are treated as pocketing areas, and intersections resulting from protrusions as islands.
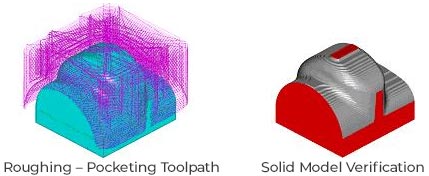
Re-Roughing – CNC Milling
The Re-Roughing methods use a specified, previously created, reference Roughing work step to automatically calculate and create a 2D Rest Curve identifying the uncut regions remaining from the reference work step. A conventional 2.5-axis curve roughing work step is then created and assigned to the Rest Curve and toolpath generated inside each region at the roughing Z Step intervals.
Finishing – CNC Milling
The Finishing Methods use three distinct toolpath generation techniques as described below.
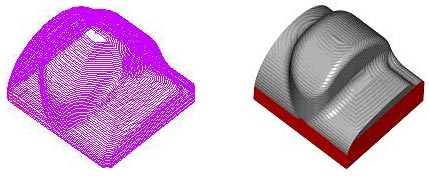
• Projection – Creates 3D toolpath by generating a 2D pattern and segmenting it into polylines based on the specified tolerance, then projecting each point to the selected Cut surfaces using the tool shape.
Re-Finishing – CNC Milling
Refinishing method allows areas uncut by a preceding workstep, due to tool size or configuration, to be identified and re-machined using an equidistant toolpath. The Refinishing workstep uses the tool and parameters of a specified reference workstep to compute the uncut area boundaries, then applies an equidistant toolpath to them using the Refinishing workstep tool
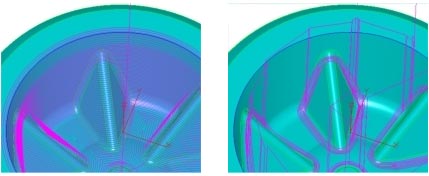
Pencil Milling – CNC Milling
The Wizard now contains a new Pencil Milling method, which generates toolpath to machine all concave surface intersections where the specified tool makes dual contact. This capability is useful for removing material remaining in corners and along fillets in both finish and semi-finishing applications. Multiple Pencil Milling worksteps using progressively smaller tools can be used to trace along part features, gradually removing remaining material.